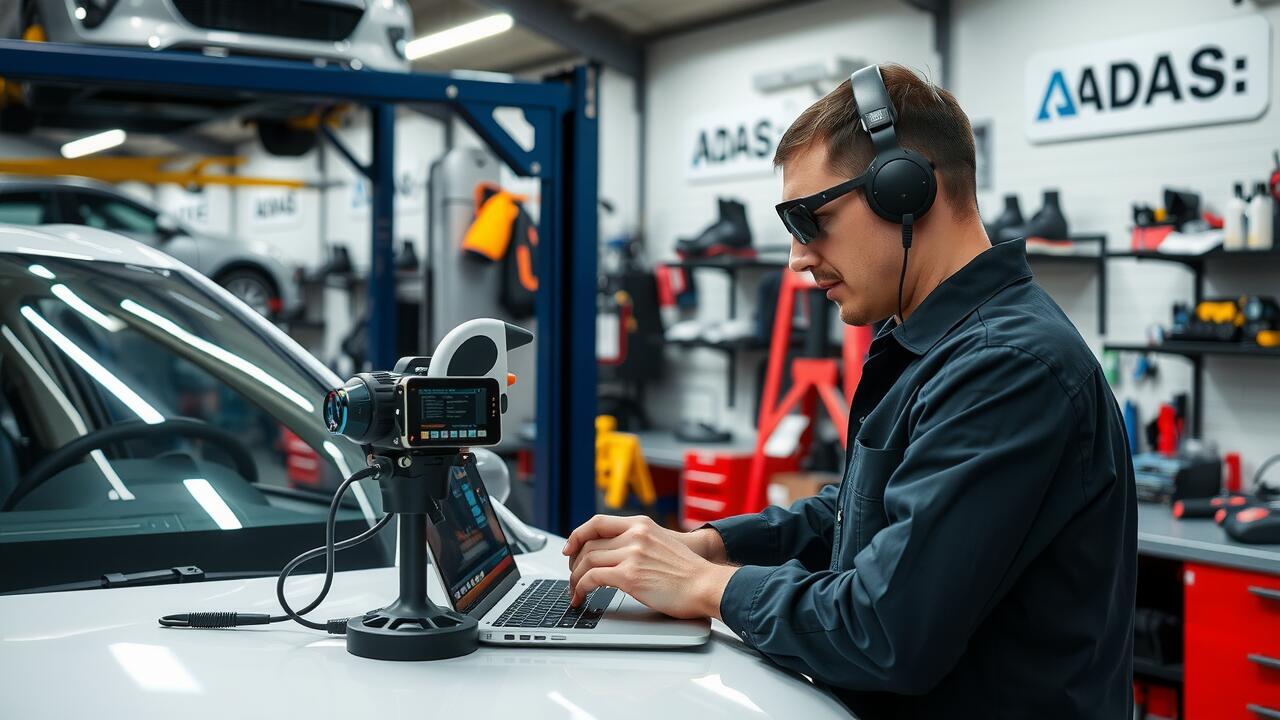
Table Of Contents
Common Challenges in Calibration
Calibration processes often encounter a range of challenges that can hinder accuracy and efficiency. One common issue is the variability in environmental conditions, which can affect measurement tools. Precision instruments can yield inconsistent results when subjected to fluctuating temperatures or humidity levels. Such inconsistencies are particularly critical in fields like automotive safety, where accurate measurements are essential for systems like ADAS recalibration.
Another significant challenge lies in the evolving technological landscape. As industries adopt advanced technologies, keeping pace with new calibration standards becomes increasingly complex. Many technicians may lack training or resources to adapt to these changes, leading to potential errors in calibration procedures. In sectors that rely heavily on technology-driven systems, successful ADAS recalibration demands up-to-date knowledge and proper equipment to ensure safety and compliance.
Issues and Solutions
Calibration processes can often encounter a range of technical and operational issues. Equipment malfunctions can lead to inaccurate measurements, creating a ripple effect on the reliability of the data collected. Operators may also face challenges pertaining to the environmental conditions during calibration, which can impact the precision of the results. An inadequate understanding of the specific calibration requirements for sophisticated systems, such as those used in automotive technology, may further complicate the process.
A practical solution to these challenges is the implementation of regular training for personnel involved in calibration tasks. This ensures that team members stay informed about the latest techniques and industry standards. In fields like automotive technology, ADAS recalibration becomes crucial after repairs or part replacements. Establishing a routine for systematic checks and audits can also mitigate errors, ensuring that equipment functions accurately and adheres to compliance regulations.
Industry Standards for Calibration
Industry standards for calibration play a critical role in ensuring reliability and accuracy across various sectors. These standards are essential for establishing protocols that organisations must follow when calibrating equipment. In industries such as automotive and healthcare, adherence to recognised standards ensures that devices perform correctly and safely. Specific requirements are outlined in guidelines from local authorities and international organisations, ensuring consistency in calibration processes.
In the automotive sector, for instance, ADAS recalibration is increasingly significant as vehicles become more technologically advanced. The calibration of Advanced Driver Assistance Systems (ADAS) must meet these stringent industry standards to guarantee optimal functionality and safety. Compliance with these standards not only enhances the performance of these systems but also instils confidence among consumers regarding the reliability of the technology integrated into modern vehicles.
Regulatory Requirements and Guidelines
Regulatory requirements for calibration remain crucial across various sectors, particularly in ensuring safety and compliance with industry standards. Organisations must adhere to specific guidelines set forth by governing bodies, aimed at maintaining quality control and accuracy in measurements. These regulations often dictate the frequency of calibration, the methods employed, and the personnel qualified to perform these tasks. This is particularly relevant in the automotive sector, where advanced driver assistance systems (ADAS) recalibration plays a vital role in vehicle safety and performance.
Compliance with these regulations is not just a matter of operational integrity; it also impacts consumer trust and brand reputation. In industries where precise measurements are critical, such as healthcare and manufacturing, failing to meet regulatory standards can lead to severe consequences. The need for meticulous adherence to guidelines is underscored by the increasing reliance on technology, making the challenges of calibration, including ADAS recalibration, all the more essential to address effectively.
Calibration in Different Fields
Calibration plays a significant role across various industries, ensuring that equipment and instruments operate within specified accuracy limits. In the automotive sector, the advancement of technology has led to the integration of sophisticated systems such as Advanced Driver Assistance Systems (ADAS). These systems rely on precise calibration to function effectively, especially after repairs or replacements. ADAS recalibration is crucial for maintaining vehicle safety and performance, aligning sensors and cameras accurately to avoid potential hazards during operation.
In the medical field, calibration is equally essential, particularly for devices that monitor vital signs and provide diagnostics. Ensuring that these instruments deliver accurate readings can directly impact patient care and treatment outcomes. Regular calibration checks help medical professionals trust their equipment, minimising the risk of errors in patient assessments. Different fields require tailored approaches to calibration, highlighting the need for industry-specific practices and standards to ensure optimal performance and safety.
Applications in Various Industries
In the automotive industry, calibration plays a crucial role in ensuring that vehicles operate safely and efficiently. Advanced Driver Assistance Systems (ADAS) have become an integral part of modern vehicles, requiring precise calibration to function correctly. The process of ADAS recalibration is necessary after repairs or when sensors are replaced, ensuring that features like lane departure warnings and adaptive cruise control operate as intended. Proper calibration not only enhances vehicle safety but also improves performance and reliability, making it essential for automotive technicians to be well-versed in the calibration processes associated with these systems.
In the medical field, calibration is vital for the accurate functioning of diagnostic equipment. Devices such as blood glucose monitors and MRI machines require regular calibration to maintain precision in measurements. The rigorous nature of the healthcare industry mandates strict adherence to calibration standards, ensuring patient safety and the reliability of test results. Similar to ADAS recalibration in vehicles, medical instrument calibration safeguards against errors that could lead to misdiagnoses or ineffective treatments. Regular monitoring and adjustment of these instruments are essential to uphold industry standards and maintain public confidence in healthcare services.
FAQS
What are the two primary methods of calibration?
The two primary methods of calibration are "comparison calibration" and "absolute calibration". Comparison calibration involves comparing the measurement of a device against a standard reference, while absolute calibration establishes a direct relationship between the measurement and a known value.
Why is calibration important in various industries?
Calibration is crucial as it ensures the accuracy and reliability of measurements, which is essential for maintaining product quality, safety standards, and compliance with regulatory requirements across different industries.
How often should calibration be performed?
The frequency of calibration depends on the specific equipment, industry standards, and the environment in which the equipment operates. Generally, calibration should be performed annually or whenever equipment is repaired, serviced, or shows signs of inaccuracy.
What challenges can arise during the calibration process?
Common challenges include environmental factors (like temperature and humidity), human error, equipment drift, and the unavailability of proper reference standards. These issues can affect measurement accuracy and consistency.
Are there regulatory standards that govern calibration practices?
Yes, various regulatory standards, such as ISO 9001 and ISO/IEC 17025, provide guidelines for calibration practices to ensure quality control in measurements and compliance with industry-specific regulations.