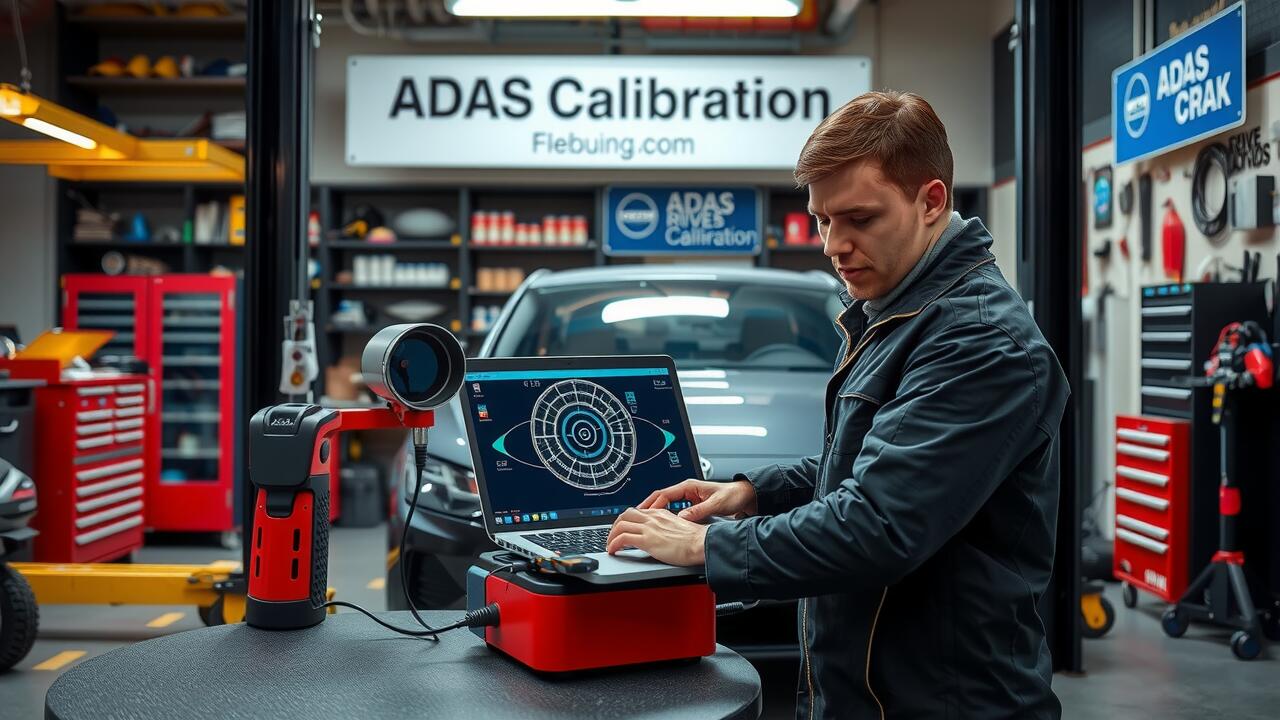
Table Of Contents
Tools and Equipment Needed for Calibration
A comprehensive set of tools and equipment is essential for effective ADAS system calibration. Basic tools often include a diagnostic scanner, which allows for communication with the vehicle's onboard computers, and alignment equipment to ensure accurate positioning. Additionally, targets specific to each vehicle model are crucial for measuring sensor alignment and performance. Having access to a calibration board can help create the necessary reference points for the sensors involved.
Safety equipment is also important when setting up for ADAS system calibration. This can include cones or markers to delineate the calibration area, ensuring that there is a safe distance from moving vehicles. A stable, open space is vital for achieving optimal results, free from obstructions that could interfere with sensor readings. Ensuring that all equipment is in good working condition will contribute significantly to a successful calibration process.
Essential Tools for a Calibration Setup
A well-equipped setup is crucial for effective ADAS system calibration. The primary tools include an alignment rack to ensure precise positioning of the vehicle, alongside laser measurement devices for accurate data collection. A calibration target is also essential, as it helps in aligning the sensors and cameras according to manufacturer specifications. Having a reliable diagnostic tool can assist in monitoring the system’s performance pre- and post-calibration, making it easier to detect any issues that may arise during the process.
In addition to the standard tools, software platforms specifically designed for ADAS system calibration play an important role. These programs help technicians identify necessary adjustments and validate the calibration results. Environmental considerations should also not be overlooked, as proper lighting and an unobstructed area enhance the accuracy of readings. A comfortable workspace further contributes to the efficiency of the calibration procedure, minimising the potential for errors due to external factors.
Calibration Procedure Overview
The calibration procedure for an Advanced Driver-Assistance Systems (ADAS) system typically involves several defined steps to ensure accuracy and functionality. Initially, technicians must confirm that the vehicle’s sensors are clean and unobstructed. This preparation phase is crucial as any dirt or interference can lead to incorrect readings. Following this, the vehicle is positioned correctly within the calibration space, which should meet specific requirements for the ADAS system calibration.
Once the vehicle is set up, specialised software is used to communicate with the vehicle's systems. Technicians will then conduct a series of tests and adjustments, monitoring data to make sure everything aligns with manufacturer specifications. In some cases, dynamic calibrations that involve driving the vehicle may be necessary. This comprehensive process ensures that the ADAS system calibration meets safety standards and performs effectively under typical driving conditions.
Step-by-Step Calibration Process
The step-by-step calibration process for an ADAS system calibration involves several crucial stages to ensure accuracy and functionality. Initial setup requires a suitable calibration environment where all essential equipment is positioned correctly. Technicians must gather specific tools, including alignment systems, targets, and diagnostic equipment, to facilitate the calibration. Identifying the vehicle’s specific requirements based on manufacturer specifications is essential to tailor the calibration procedure accordingly.
Once the tools are in place, the calibration begins with the vehicle being prepared, which often includes aligning the vehicle's wheels and ensuring it is at the correct height. Following this, technicians will conduct a series of diagnostic tests to confirm the current state of the ADAS components. Each component, such as cameras and sensors, is systematically tested and adjusted as needed. After adjustments are made, a final round of testing is conducted to validate the calibration results, ensuring the system operates within the required parameters.
Common Challenges in Space Allocation
Inadequate space can pose significant challenges for ADAS system calibration. Limited room may hinder technicians' ability to set up equipment properly or manoeuvre vehicles safely during the calibration process. When there isn't enough space to ensure the vehicle's sensor systems are adequately aligned with calibration targets, the accuracy of the calibration can be compromised. This can lead to prolonged calibration times and increased likelihood of errors, which could affect vehicle performance once back on the road.
Environmental factors can also complicate space allocation for ADAS system calibration. For instance, outdoor calibration may be influenced by varying weather conditions such as rain or bright sunlight. Alternatively, indoor calibration facilities that lack sufficient height or clearance might restrict the full articulation of certain vehicles, impeding proper calibration procedures. Technicians must consider these factors when designing calibration setups to ensure efficiency and safety in the overall process.
Issues Faced During Calibration Setup
Setting up for ADAS system calibration often presents numerous challenges, particularly concerning space allocation. Limited workshop space can obstruct the movement of vehicles and calibration equipment, leading to potential inaccuracies in the calibration process. Adequate room is crucial for the consistent positioning of calibration targets and equipment required to perform the calibration effectively. When the environment is cramped, technicians may struggle to adhere to the specific guidelines that ensure precise readings and adjustments.
Environmental factors also play a significant role in the calibration setup for ADAS systems. Calibration often requires specific lighting conditions and minimal interference from surrounding objects. Inadequate space can lead to unwanted reflections or obstructions that affect sensor alignment. Furthermore, any variation in surface conditions, such as uneven flooring or cluttered areas, may compromise the integrity of the calibration, resulting in calibration errors that could negatively impact vehicle performance.
FAQS
What is ADAS calibration?
ADAS calibration involves adjusting and aligning the sensors and cameras of Advanced Driver Assistance Systems to ensure they function accurately and effectively.
How much space is typically required for ADAS calibration?
The space required for ADAS calibration can vary, but generally, a minimum of 25 to 35 feet in length and 10 to 15 feet in width is recommended to accommodate the vehicle and equipment effectively.
Can I perform ADAS calibration in a regular garage?
While it may be possible to perform ADAS calibration in a regular garage, it’s important to ensure there is sufficient space, proper lighting, and a level surface to meet calibration requirements.
What tools and equipment are necessary for ADAS calibration?
Essential tools include calibration targets, a laser alignment tool, diagnostic equipment, and a computer with calibration software specific to the vehicle make and model.
What are common challenges faced during ADAS calibration setup?
Common challenges include inadequate space for calibration targets, improper lighting conditions, and difficulties in accessing the vehicle's sensors and systems due to space constraints.